Bearing Types and Application Design
Bearing Engineering & Applications
Related Resources:
There are many different types of bearings.
Bearing Type |
Description |
Friction |
Bearing Stiffness |
Velocity |
Life Span |
Comments |
|
Plain Bearing | Plain bearingRubbing surfaces, usually with lubricant; some bearings use pumped lubrication and behave similarly to fluid bearings. | Depends on materials and construction, PTFE has coefficient of friction ~0.05-0.35, depending upon fillers added | Good, provided wear is low, but some slack is normally present | Low to very high | Low to very high - depends upon application and lubrication | Widely used, relatively high friction, suffers from stiction in some applications. Depending upon the application, lifetime can be higher or lower than rolling element bearings. | |
Ball or Roller Bearing | Rolling element bearingBall or rollers are used to prevent or minimise rubbing | Rolling coefficient of friction with steel can be ~0.005 (adding resistance due to seals, packed grease, preload and misalignment can increase friction to as much as 0.125) | Good, but some slack is usually present | Moderate to high (often requires cooling) | Moderate to high (depends on lubrication, often requires maintenance) | Used for higher moment loads than plain bearings with lower friction | |
Jewel Bearing | Jewel bearingOff-center bearing rolls in seating | Low | Low due to flexing | Low | Adequate (requires maintenance) | Mainly used in low-load, high precision work such as clocks. Jewel bearings may be very small. | |
Magnetic Bearing | Fluid bearingFluid is forced between two faces and held in by edge seal | Zero friction at zero speed, low | Very high | Very high (usually limited to a few hundred feet per second at/by seal) | Virtually infinite in some applications, may wear at startup/shutdown in some cases. Often negligible maintenance. | Can fail quickly due to grit or dust or other contaminants. Maintenance free in continuous use. Can handle very large loads with low friction. | |
Fluid or Hydrodynamic Bearing | Magnetic bearingsFaces of bearing are kept separate by magnets ( electromagnets or eddy currents ) | Zero friction at zero speed, but constant power for levitation, eddy currents are often induced when movement occurs, but may be negligible if magnetic field is quasi-static | Low | No practical limit | Indefinite. Maintenance free. (with electromagnets ) | Active magnetic bearings (AMB) need considerable power. Electrodynamic bearings (EDB) do not require external power. | |
Flexure Bearings | Flexure bearingMaterial flexes to give and constrain movement | Very low | Low | Very high. | Very high or low depending on materials and strain in application. Usually maintenance free. | Limited range of movement, no backlash, extremely smooth motion | |
† Stiffness is the amount that the gap varies when the load on the bearing changes, it is distinct from the friction of the bearing. |
! knife edge bearings
Other bearing types:
- Deep groove ball bearings
- Y-bearings
- Angular contact ball bearings
- Self-aligning ball bearings
- Cylindrical roller bearings
- Full complement cylindrical roller bearings
- Needle roller bearings
- Tapered roller bearings
- Spherical roller bearings
- Toroidal bearings
- Bearing types
- Thrust ball bearings
- Angular contact thrust ball bearings
- Cylindrical roller thrust bearings
- Needle roller thrust bearings
- Tapered roller thrust bearings
- Spherical roller thrust bearings
- Track runner bearings
- Cam rollers
- Support rollers
- Cam followers
The most common bearing application is the Ball Bearing
Ball Bearing types permit smooth, low-friction movement between two or more surfaces. This movement is either rotary (shaft rotating within a mount) or linear (one surface moving along another). Bearings , are anti-friction devices, each having different anti-friction characteristics. By far the largest number of bearings are oil-lubricated. The oil film can be maintained through pumping by a pressurization system (pump). Or it can be maintained by a squeezing or wedging of lubricant produced by the rolling action of the bearing itself.
General Application Guidelines:
Ball bearings are the less expensive choice in the smaller sizes and under lighter loads, while roller bearings are less expensive for larger sizes and heavier loads.
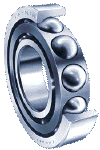
Roller bearings are more satisfactory under shock or impact loading than ball bearings.
Ball-thrust bearings are for pure thrust loading only. At high speeds, a deep-groove or angular-contact ball bearing usually will be a better choice, even for pure thrust loads.
Self-aligning ball bearings and cylindrical roller bearings have very low friction coefficients.
Deep-groove ball bearings are available with seals built into the bearing so that the bearing can be pre-lubricated to operate for long periods reducing maintenance requirements.
Careful consideration of speed requirements are important for proper bearing application design. Useable speeds are influenced by bearing size, properties, lubrication and operating temperatures. The permissible speed varies inversely with mean bearing diameter.
Ball Bearing Useable Life
Ball bearings were formerly rated on the basis of the compressive stress in the most heavily loaded ball. Except for static loads, experience has shown that the actual cause of failure is fatigue. Fatigue characteristics are used for load rating and are dependent on experimental results. Analytical methods are available to determine a particular bearings useable life. Consult with manufacturer to determine typical bearing performance characteristics.
The life of a ball bearing is the life in hours at some known speed, or the number of revolutions, that the bearing will attain before the first evidence of fatigue appears on any of the moving elements. Experience has shown that the life of an individual ball bearing cannot be precisely predicted. Fatigue characteristics are used for load ratings.
Even if bearings are properly installed, adequately lubricated, protected from foreign matter, and are not subjected to extreme operating conditions, they can ultimately fatigue. Under ideal conditions, the repeated stresses developed in the contact areas between the balls and the raceways eventually can result in fatigue of the material which results in spalling of the bearing load carrying surfaces. In most applications, the fatigue life is the maximum useful life of a bearing.